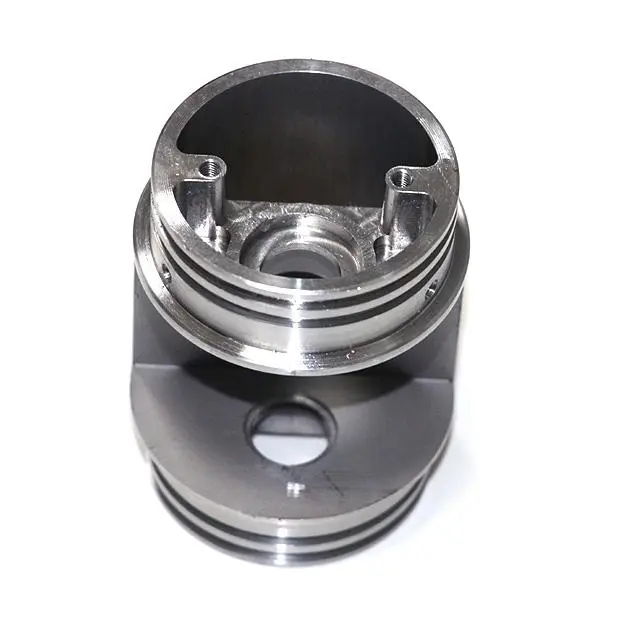
- +8615586668226
- [email protected]
- No. 30, Hongbang Industrial Park, Shenzhen
This guide delves into the importance of surface roughness, how it is measured, and how manufacturers can use surface finish charts to ensure the best results for their products.
Surface finish refers to the texture and quality of a material’s surface, which can be altered through various processes like removing, reshaping, or adding material. The key components of surface finish include roughness, waviness, and lay, which define the overall texture of the surface.
Roughness measures the small, closely spaced irregularities on a surface. Waviness represents larger undulations, and lay refers to the direction of the surface pattern. When machinists refer to surface finish, they usually mean surface roughness.
Surface finish impacts how a product performs under various conditions. Products with the correct surface finish will be more durable, resistant to wear, and have better performance characteristics, such as corrosion resistance, improved adhesion for coatings, and enhanced electrical conductivity. Maintaining the appropriate surface finish helps ensure consistency and reliability in manufacturing.
Surface roughness is typically measured using the Ra value (Roughness Average), which calculates the average height of surface peaks and valleys. Several methods exist for measuring roughness, including direct measurement with a stylus, non-contact techniques using light or sound, comparison methods with reference samples, and in-process techniques that measure roughness during production.
There are three primary ways to measure surface roughness:
Surface roughness charts help manufacturers standardize the texture of their parts. Common parameters used include Ra (Roughness Average), Rmax (Vertical Distance from Peak to Valley), and Rz (Average Maximum Height of the Profile). Each parameter gives different insights into the surface quality, helping to identify potential issues like burrs or scratches.
Surface roughness charts provide a reference for manufacturers to ensure parts meet specific quality standards. These charts convert different roughness measurements and show how various processes affect surface texture. The most commonly used parameters include Ra, RMS (Root Mean Square), and CLA (Center Line Average).
For quick reference, here are common surface roughness ratings and their applications:
Surface roughness directly impacts the performance and quality of manufactured parts. By understanding surface finish and using surface roughness charts, manufacturers can ensure their products meet the required standards for durability, performance, and appearance. Maintaining precise surface roughness is challenging, but with the right tools and techniques, manufacturers can optimize their processes for success.
We specialize in delivering top-tier surface finishing services to meet all your manufacturing needs. Whether you need anodizing, polishing, or bead blasting, our team of experts is ready to help you achieve the perfect surface finish for your products.
Get the latest trends and facts about CNC fabrication from our blog.
Shenzhen Runkey Precision Technology Co. Ltd, a subsidiary of the Tensun Group, is your trusted one-stop solution for custom manufacturing from prototyping to production.Transforming your idea into reality with digital manufacturing resources,streamlined processes, expert guidance,accelerated timelines, and uncompromising quality.
©2024. CNC Fabrication All Rights Reserved.