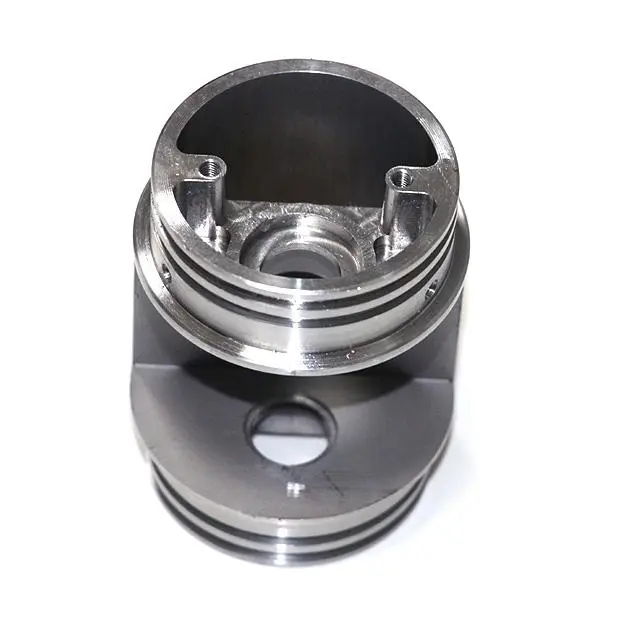
- +8615586668226
- [email protected]
- No. 30, Hongbang Industrial Park, Shenzhen
A countersink is a conical hole cut into a metal piece to allow the screw head to sit flush with or below the surface of the material. This process enhances the integrity and appearance of the assembled product.
The countersink hole in metal workpieces is a fundamental aspect of modern manufacturing, critical for sheet metal fabrication and more.
Using a countersink facilitates several advantages in metal and sheet metal assembly processes:
Incorporating countersinking is essential for industries requiring sleek finishes and reliable assemblies, such as electronics and consumer products.
Various countersink tools are designed for specific applications, each serving different purposes:
Countersink Drill Bit
Countersink Cutters
Understanding these tools aids in selecting the right equipment for your countersinking needs, ensuring optimal results.
Selecting the correct countersink drill bit involves consideration of several factors:
Matching your drill bit to the specific requirements of your project ensures precision and durability, enhancing production efficiency.
Several standard countersink angles are used in the industry, each catering to specific screw types and applications:
Countersink Angle | Common Applications |
---|---|
82 Degrees | Often used for machine screws |
90 Degrees | Standard for crosshead screws |
100 Degrees | Utilized for rivets and specialty fasteners |
Choosing the right countersink angle is crucial to accommodate a screw head effectively, ensuring a seamless fit and finish.
Drilling a pilot hole is important for countersinking, especially in metal workpieces:
A pilot hole ensures accuracy, integrity, and quality of the resulting countersink hole.
Creating a perfectly countersink hole in metal involves strategic steps:
Select the Right Drill Bit
Drill the Pilot Hole
Create the Countersink Hole
Mastering these steps ensures each hole in metal meets both aesthetic and functional requirements.
Several challenges may arise during the countersinking process:
Solutions: Always measure and adjust settings before drilling to ensure precision and avoid common pitfalls.
The versatility of countersinking extends across numerous applications:
The wide-ranging applications of countersinking highlight its importance in quality manufacturing processes.
What is the purpose of a countersink?
A countersink creates a conical hole that allows for the screw head to sit flush with the surrounding material, enhancing both functionality and appearance.
Is it challenging to countersink a screw in metal?**
Countersinking in metal requires precise technique but yields professional results when correct tools and methods are applied.
What materials are best suited for countersink tools?
Carbide and high-speed steel are excellent choices for countersink drill bits used in harder metal applications.
How can I avoid common countersink mistakes?
Properly drill a pilot hole and choose the correct countersink angle to prevent errors such as misalignment or overcutting.
Why is drilling a pilot hole important before countersinking?
A pilot hole guides the countersink drill bit, ensuring consistent results and preventing damage to the metal workpiece.
Our CNC Fabrication Manufacturing Plant is dedicated to delivering quality machining solutions for industries ranging from automotive to medical devices. Uncover our capabilities:
Ready to enhance your production process with expert countersinking techniques? Contact us today to explore our services.
Get the latest trends and facts about CNC fabrication from our blog.
Shenzhen Runkey Precision Technology Co. Ltd, a subsidiary of the Tensun Group, is your trusted one-stop solution for custom manufacturing from prototyping to production.Transforming your idea into reality with digital manufacturing resources,streamlined processes, expert guidance,accelerated timelines, and uncompromising quality.
©2024. CNC Fabrication All Rights Reserved.