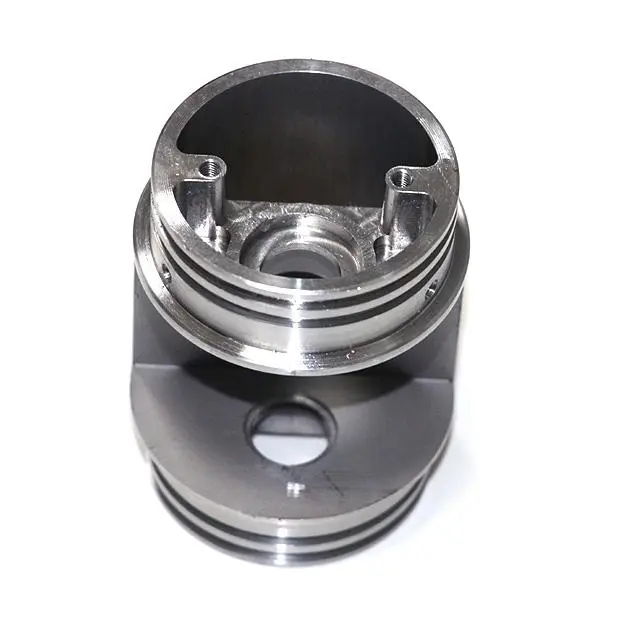
- +8615586668226
- [email protected]
- No. 30, Hongbang Industrial Park, Shenzhen
Wire EDM, or Wire Electrical Discharge Machining, is a process where metal is shaped using a series of electric sparks. This process is ideal for cutting intricate and precise shapes in conductive materials.
Wire EDM is instrumental for creating parts that require high precision and minimal surface roughness.
The journey of electrical discharge machining began in the mid-20th century.
Learning the history of EDM highlights its revolutionary impact on manufacturing.
Wire EDM offers several advantages over traditional machining methods.
Wire EDM | Conventional Machining |
---|---|
Uses electric discharges | Uses physical contact cutting tools |
Can machine complex shapes | Limited in intricate cuts |
No tool wear on the wire | Tool wear is a concern |
Wire EDM is the go-to technique for machining intricate parts without the constraints that conventional machining faces.
Delving into the complexities of the wire EDM process offers insight into its efficiency.
This machining process stands out for its ability to produce complex geometries with high precision.
There are several types of EDM machines, each suited for particular applications.
Choosing the correct type of machine is crucial for meeting your project requirements.
Manufacturers across various sectors benefit significantly from wire EDM.
Our Wire EDM services exemplify these benefits, delivering high-quality results tailored to client needs.
Small hole EDM specializes in drilling tiny holes with unparalleled precision.
Small hole EDM supports the manufacturing of components that require miniature features with accuracy.
Dielectric fluids play a critical role in the EDM process.
Understanding the role of these fluids reveals the importance of maintaining the perfect cutting environment.
Understanding the key differences between wire EDM and sinker EDM helps in decision-making.
Aspect | Wire EDM | Sinker EDM |
---|---|---|
Cutting Type | Uses a moving wire to cut | Uses a shaped electrode to sink into material |
Applications | Thinner, more intricate parts | Deep cavities and complex shapes |
Material Contact | No direct contact | Ends of electrodes apply spark erosion |
Choosing between them depends on your specific project needs.
Enlisting professional EDM services ensures quality and efficiency.
Our Wire EDM Services aim to elevate your manufacturing projects with reliability and skill.
What is the primary use of wire EDM?
Wire EDM is primarily used for cutting intricate and precise shapes in conductive materials, especially when high precision is required.
How does wire EDM differ from traditional cutting methods?
Wire EDM does not require direct contact between the tool and workpiece, using electrical sparks instead, allowing for more complex shapes without tool wear.
Can wire EDM handle all types of metals?
Wire EDM is suitable for any conductive material, including metals like steel, aluminum, and even hard-to-machine alloys.
What industries benefit the most from wire EDM?
Industries such as aerospace, automotive, medical devices, and electronics heavily rely on wire EDM for precision manufacturing.
Is wire EDM environmentally friendly?
Yes, wire EDM is considered environmentally friendly as it minimizes material waste and the use of dielectric fluids like deionized water reduces the environmental impact.
For more information on how we can assist with your EDM needs, explore our Machining Services or contact us today. Discover the precision and excellence that our CNC solutions can bring to your manufacturing projects.
Harness the capabilities of wire EDM with us. Let’s create excellence together.
Get the latest trends and facts about CNC fabrication from our blog.
Shenzhen Runkey Precision Technology Co. Ltd, a subsidiary of the Tensun Group, is your trusted one-stop solution for custom manufacturing from prototyping to production.Transforming your idea into reality with digital manufacturing resources,streamlined processes, expert guidance,accelerated timelines, and uncompromising quality.
©2024. CNC Fabrication All Rights Reserved.