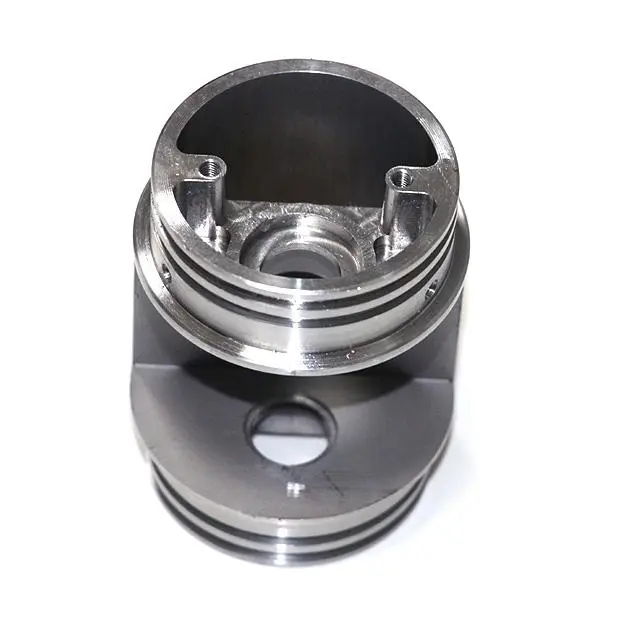
- +8615586668226
- [email protected]
- No. 30, Hongbang Industrial Park, Shenzhen
Precision in manufacturing refers to the consistency of repeated measurements and processes. In CNC machining, achieving high precision means that the output is reliably replicable, creating high precision and accurate components that meet stringent specifications.
Importance of Precision:
Precision ensures that your manufacturing outcomes align closely with design specifications, which is vital for maintaining good machining precision in diverse applications.
Accuracy deals with how close a measurement is to the true or accepted value. In CNC machining, this indicates the degree to which a finished product conforms to its design dimensions.
Significance of Accuracy:
Ensuring accuracy in part production involves aligning your machinery and processes to consistently produce parts that meet exacting standards.
Understanding the difference between precision and accuracy is key to improving CNC machining processes:
These concepts are interrelated; a machine can be precise without being accurate and vice versa. Identifying whether your challenge lies in precision or accuracy can direct corrective measures effectively.
Precision in CNC machining is achieved through tight control over the machining process. It involves the careful calibration of machines to ensure that every cut, hole, and shape adheres to predetermined specifications without deviation.
At CNC Machining, utilizing tools like precision fixtures and precision measuring equipment allows us to maintain the highest standards in CNC operations, vital for achieving optimal machining outcomes.
Investing in high precision and accuracy yields numerous advantages:
Such benefits underscore the importance of focusing on these factors to drive excellence in precision machining services.
To improve precision and accuracy:
By adopting these practices, manufacturing plants can enhance the precision and accuracy in part production, ensuring that every component produced meets the required specifications.
Tolerance defines the permissible limit of variation in a physical dimension. It’s crucial in determining how much deviation is acceptable without compromising the part’s precision or functionality.
Key Aspects:
Understanding and setting appropriate tolerances is vital for achieving high precision and machining accuracy in diverse applications.
To measure precision effectively:
Ensuring reliability in precision ensures your products meet both internal standards and customer expectations, enhancing the overall accuracy in manufacturing processes.
Common issues include:
Identifying these challenges early allows for prompt corrective action, improving the machining process and ensuring good machining accuracy.
How do precision and accuracy affect CNC machining?
Can precision exist without accuracy?
Why is CNC machining preferred for high precision?
What role does software play in enhancing precision?
Explore our tailored CNC solutions for more insights into enhancing your precision machining capabilities, or contact our team for customized support. Let us help you master the balance of precision vs. accuracy in your production processes.
Get the latest trends and facts about CNC fabrication from our blog.
Shenzhen Runkey Precision Technology Co. Ltd, a subsidiary of the Tensun Group, is your trusted one-stop solution for custom manufacturing from prototyping to production.Transforming your idea into reality with digital manufacturing resources,streamlined processes, expert guidance,accelerated timelines, and uncompromising quality.
©2024. CNC Fabrication All Rights Reserved.