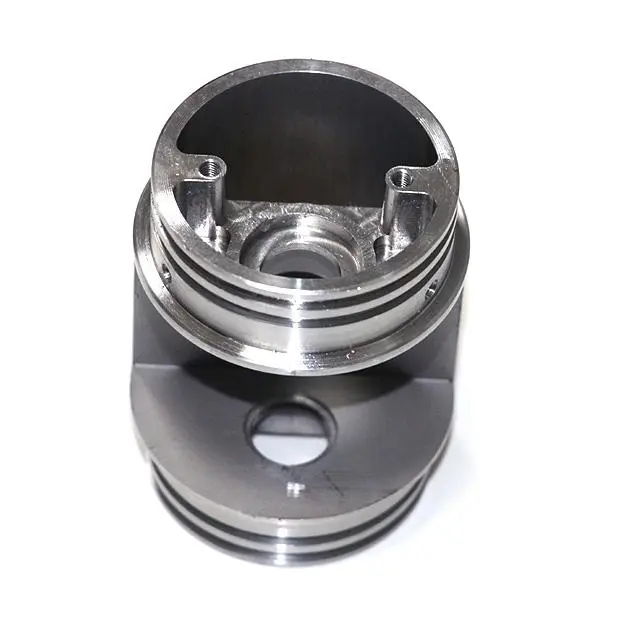
- +8615586668226
- [email protected]
- No. 30, Hongbang Industrial Park, Shenzhen
Physical Vapor Deposition (PVD) is a method used to deposit thin films of material onto various substrates. This process involves the transformation of a material from a solid into vapor and then its condensation onto a substrate. As an advanced deposition technique, PVD is valued for its ability to create uniform and high-quality coatings.
Parameter | PVD Coating | Traditional Coating |
---|---|---|
Environmentally Friendly | Yes | No |
Coating Uniformity | Excellent | Moderate |
Deposition Speed | High | Varies |
The PVD coating process involves several steps: heating the coating material, evaporating it in a vacuum environment, and then allowing it to condense on the substrate. This physical process ensures a uniform coating and is advantageous for decorative applications.
Benefits of PVD include improved durability, enhanced aesthetics, and better resistance to corrosion. This makes PVD a preferable choice in many industrial applications where high performance is critical.
“PVD coatings have revolutionized industries by offering exceptional performance with reduced environmental footprint,” a leading industry analyst remarks.
The application of PVD spans a wide range of industries, providing solutions that enhance both function and form.
Industry | Application |
---|---|
Aerospace and Aviation | Engine components |
Medical Devices | Surgical instruments |
Automotive | Decorative trim, wheels |
Electronics | Circuit components |
Defense and Military | Armor, shields |
Energy and Renewable Energy | Solar panels, turbines |
PVD and CVD (Chemical Vapor Deposition) are both thin-film deposition techniques. However, they differ fundamentally in their mechanisms and applications.
Process | PVD | CVD |
---|---|---|
Temperature | Lower | Higher |
Environmental Impact | Minimal | Can involve harmful chemicals |
Typical Use Cases | Decorative, functional coatings | Semiconductors |
Understanding the advantages and disadvantages of PVD is crucial for selecting the right coating process for your product.
Performance of PVD Coating:
Various types of PVD coating processes include sputtering, evaporation, and arc vapor deposition. Each has its own set of benefits and ideal applications.
Selecting the most appropriate PVD coating involves evaluating the specific applications and desired properties of the coating material.
Optimizing the performance of PVD coatings requires understanding the fundamental processes and ensuring precise control.
What does PVD stand for?
PVD stands for Physical Vapor Deposition, a technique for depositing thin films onto various substrates.
How does PVD improve product durability?
PVD coatings form a hard, protective layer that resists wear and corrosion, extending product lifespan.
Can PVD be used on all materials?
While versatile, PVD is most effective on materials that can withstand vacuum environments and elevated temperatures.
Is PVD environmentally friendly?
Yes, PVD is considered an environmentally friendly process, as it does not involve harmful chemicals.
What industries benefit most from PVD?
Industries like aerospace, automotive, and medical devices gain significantly from the durability and precision of PVD coatings.
Explore more on our Machining Services or get detailed insights into Fabrication Services. To enhance your knowledge on advanced solutions, visit our CNC Solutions. Discover specialized applications in Aerospace and Robotics.
Get the latest trends and facts about CNC fabrication from our blog.
Shenzhen Runkey Precision Technology Co. Ltd, a subsidiary of the Tensun Group, is your trusted one-stop solution for custom manufacturing from prototyping to production.Transforming your idea into reality with digital manufacturing resources,streamlined processes, expert guidance,accelerated timelines, and uncompromising quality.
©2024. CNC Fabrication All Rights Reserved.