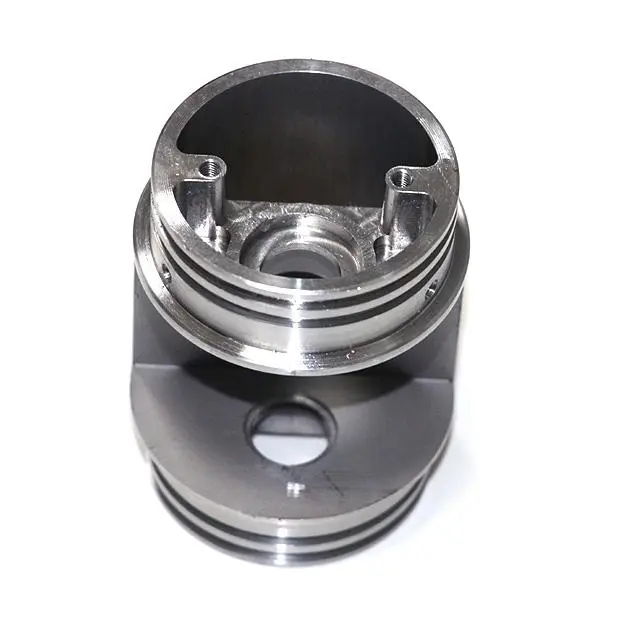
- +8615586668226
- [email protected]
- No. 30, Hongbang Industrial Park, Shenzhen
CNC machines (Computer Numerical Control) are automated tools that precisely control the movement of a cutting tool to shape materials. These machines play a pivotal role in modern manufacturing.
CNC machines provide precision and efficiency, reducing errors and improving consistency in the production process.
Precision in machining is vital for ensuring that parts meet exact specifications and function correctly.
Incorporating precision in manufacturing processes is essential for companies aiming for competitiveness and sustainability.
A CNC milling machine is designed with several key components that ensure precision and accuracy:
Understanding these components and their roles helps manufacturers utilize milling machines effectively for high-precision tasks.
Optimization of the milling process involves strategic steps to enhance the accuracy and precision of CNC operations.
These steps are vital for optimizing machining conditions, which ensure accuracy and improved machining results.
To consistently achieve high precision and accuracy, adherence to best practices in CNC operations is crucial.
Employing these practices helps maintain the accuracy and precision needed for exceptional production outcomes.
Incorporating advanced machining techniques can significantly enhance the precision in CNC milling.
Using these techniques enables manufacturers to tackle more complex machining tasks efficiently and with higher precision.
Even with state-of-the-art machinery, achieving precision can present challenges:
Understanding these challenges and implementing solutions such as regular tool inspections and robust coding practices are key to overcoming them.
Precision machining is applied across diverse sectors, showcasing its versatility and importance:
By harnessing precision machining, manufacturers can meet the specialized demands of industries serving aerospace to consumer products.
Why is precision important in CNC machining?
Precision ensures that each part meets strict specifications, reducing waste and improving product reliability and performance.
What techniques increase precision in milling?
Techniques like 5-axis milling and high-speed machining enhance precision by enabling more accurate and flexible machining operations.
How does material choice affect precision?
Different materials react uniquely to machining. Understanding their properties helps select the appropriate tools and parameters, ensuring precision and quality.
What maintenance practices help maintain machine precision?
Regularly inspecting and maintaining CNC machines preserves their capability to perform with exceptional precision and accuracy.
Can advanced software improve precision?
Yes, modern CNC software enables precise control over machine tools, enhancing the accuracy and precision of CNC operations.
For high precision machining solutions tailored to your industry needs, our CNC Fabrication Manufacturing Plant provides unmatched excellence. Discover:
Ready to elevate your machining projects with precision? Contact us to learn how we can meet your needs.
Get the latest trends and facts about CNC fabrication from our blog.
Shenzhen Runkey Precision Technology Co. Ltd, a subsidiary of the Tensun Group, is your trusted one-stop solution for custom manufacturing from prototyping to production.Transforming your idea into reality with digital manufacturing resources,streamlined processes, expert guidance,accelerated timelines, and uncompromising quality.
©2024. CNC Fabrication All Rights Reserved.