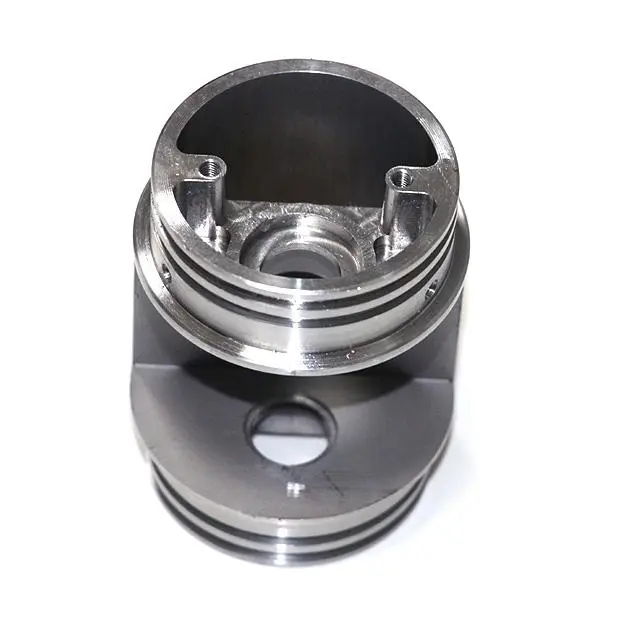
- +8615586668226
- [email protected]
- No. 30, Hongbang Industrial Park, Shenzhen
Inconel is a family of nickel-chromium-based alloys known for their ability to withstand extreme environments. These Inconel alloys are particularly valued for their resistance to oxidation and high temperatures, making them ideal for high-temperature applications.
Understanding the superior performance characteristics of Inconel is crucial for leveraging its unique advantages in various industrial sectors.
Inconel machining is notoriously challenging due to its toughness and work hardening properties. These qualities result in several machining difficulties:
The inherent nature of Inconel poses significant challenges to machinists, necessitating a strategic approach for success.
Inconel 625 and 718 are among the most popular Inconel grades used in machining applications due to their distinct properties:
Inconel 625
Inconel 718
These different grades of Inconel demand specific machining techniques tailored to their unique characteristics.
Selecting the right cutting tool is crucial when machining Inconel. High-quality tools designed to withstand significant heat generation during machining are a must.
The combination of superior tool materials and appropriate machining parameters is the key to successful Inconel machining.
Achieving optimal results in Inconel machining requires careful selection and optimization of machining parameters.
Optimizing the machining parameters is essential for maintaining the quality and efficiency of the machining operation.
Advanced tips for machining Inconel involve specialized methods to handle its complexities effectively.
Embracing these techniques for machining Inconel allows manufacturers to overcome its notorious machining challenges efficiently.
Work hardening and excessive heat generation during machining can undermine the quality of Inconel parts.
A nuanced approach to mitigating work hardening and heat issues improves both the machining process and end product quality.
Aerospace applications are the most notable users of machined Inconel parts, given their performance characteristics.
Inconel parts often justify the challenges of machining due to the immense benefits they offer in such demanding applications.
Maintaining the highest quality of Inconel machining involves comprehensive monitoring and precision control during every step.
Mastering Inconel machining ensures high-quality output essential for industries that depend on the integrity of high-performance components.
What makes Inconel stand out in high-temperature environments?
Inconel’s composition offers exceptional corrosion resistance and maintains its strength at elevated temperatures, making it ideal for high-temperature applications.
Why is machining Inconel considered challenging?
The rigidity required for Inconel machining and its tendency to work harden makes it demand specialized tools and techniques.
Which Inconel grades are most commonly machined?
Inconel 625 and 718 are frequently used due to their specific strength and performance traits in diverse applications.
How does one manage the heat generated during machining Inconel?
Utilizing effective cooling systems and optimizing machining parameters can control the heat generation and extend tool life.
Can standard cutting tools be used for machine inconel?
No, machining Inconel requires specialized equipment such as carbide tools with advanced coatings to withstand the material’s challenges.
Our CNC Fabrication Manufacturing Plant offers industry-leading services tailored for high-performance materials like Inconel. Explore more about our capabilities:
Optimize your Inconel machining operations with us. Contact us today to learn how we can support your manufacturing projects.
Get the latest trends and facts about CNC fabrication from our blog.
Shenzhen Runkey Precision Technology Co. Ltd, a subsidiary of the Tensun Group, is your trusted one-stop solution for custom manufacturing from prototyping to production.Transforming your idea into reality with digital manufacturing resources,streamlined processes, expert guidance,accelerated timelines, and uncompromising quality.
©2024. CNC Fabrication All Rights Reserved.