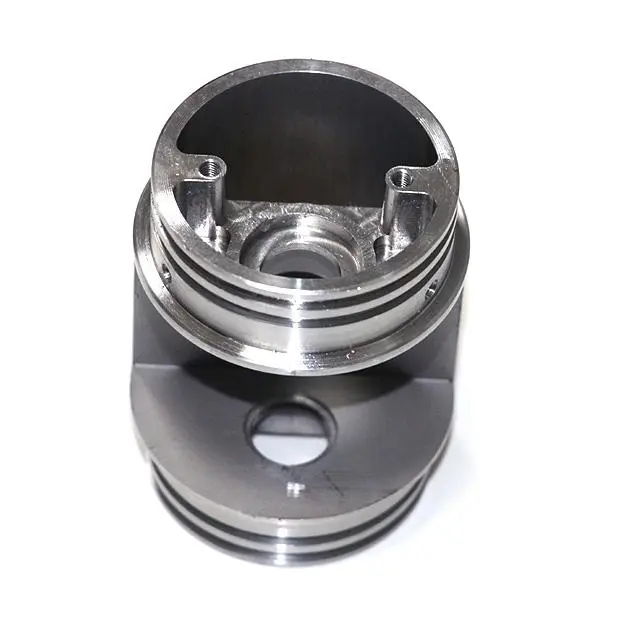
- +8615586668226
- [email protected]
- No. 30, Hongbang Industrial Park, Shenzhen
Their ability to provide strong, permanent connections with minimal installation access makes them a preferred choice across various industries. Available in a variety of materials, such as aluminum, stainless steel, and copper, rivets serve numerous applications. This guide will cover the installation process, materials used, and the types of rivets commonly employed.
A rivet is a permanent mechanical fastener used to join multiple parts. Each rivet consists of three main components: a head, a shank, and a tail. To install a rivet, it is inserted into a slightly oversized hole and then permanently deformed through compressive force. This deformation is achieved using tools that vary depending on the type of rivet.
Typically, rivets are installed using pneumatic or manual hammering, hydraulic pressing, or handheld rivet guns. When choosing rivet sizes, it’s important to consider the grip length and hole size, as rivets are available in different grip lengths for various sheet thicknesses. While aluminum and steel are the most common materials for rivets, copper is also used. Industries such as automotive, aerospace, construction, and manufacturing frequently utilize rivets for their fastening needs.
Rivets can be crafted from various materials, each suited for specific applications:
Care must be taken when selecting rivet materials to prevent galvanic corrosion when fastening dissimilar materials.
Different types of rivets are designed for specific applications, as listed below:
Blind Rivets (Pop Rivets): These are used when access is limited to one side. Installed using a rivet gun, the shank is deformed by pulling on the stem, which snaps off at a predetermined force.
Solid Rivets: Among the oldest rivet types, solid rivets are placed into a pre-drilled hole and deformed using a hammer or rivet gun. They are used in critical applications, such as in vehicle bodies and bridges.
Tubular Rivets: Similar to solid rivets, tubular rivets feature a hole along the shaft, allowing for easier installation as only the thin walls need to flare outwards.
Drive Rivets: Comprising a short shank with a protrusion, these rivets are installed by hammering the protrusion to deform the shank, making them useful for commercial sheet metal work.
Split Rivets: These light-duty rivets have a split shaft that is separated and flattened against the rear component during installation. They are often used in plastics and textiles.
Self-Piercing Rivets: These rivets do not require pre-drilled holes and pierce through the top sheet into the second sheet, creating a strong connection without passing completely through. They are commonly used in aerospace applications.
Rivets offer several benefits:
Despite their benefits, rivets have some drawbacks:
Rivets are a reliable and efficient method for joining components in various industries, offering significant advantages in terms of installation speed and cost. However, it is essential to consider their limitations, particularly regarding permanence and sealing capabilities. When selecting rivets, understanding the specific application and material compatibility is crucial for ensuring optimal performance. Whether you need to join components using rivets or other methods, our services can help with CNC machining, die casting and more. We pride ourselves on delivering high-quality parts on time, with a robust quality management system in place. Our AI-powered DFM feedback and instant pricing make it easy to get complex parts delivered quickly. Let’s Discuss Together!
Get the latest trends and facts about CNC fabrication from our blog.
Shenzhen Runkey Precision Technology Co. Ltd, a subsidiary of the Tensun Group, is your trusted one-stop solution for custom manufacturing from prototyping to production.Transforming your idea into reality with digital manufacturing resources,streamlined processes, expert guidance,accelerated timelines, and uncompromising quality.
©2024. CNC Fabrication All Rights Reserved.