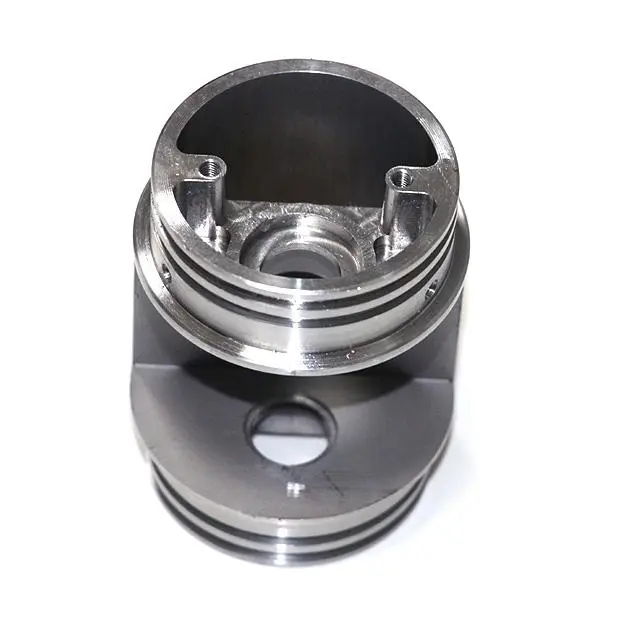
- +8615586668226
- [email protected]
- No. 30, Hongbang Industrial Park, Shenzhen
Tapped and threaded holes are common terms, but they often cause confusion. This article will clarify these concepts, explore the processes behind tapping and threading, and help you understand when to use each term correctly.
Tapping is the process of creating internal threads inside a hole to accommodate a screw or bolt. A tapped hole is simply a hole with internal threads. To start the tapping process, a hole is drilled slightly smaller than the major diameter of the threaded fastener to be used. Here’s the formula for determining the correct drill size for ANSI threads:
Drill Size = Major thread diameter – (1 ÷ # threads per inch) + 0.005″ (if pitch > 10), 0.000″ (if pitch ≤ 10)
Once the hole is drilled, a tap is used to form threads on the inside. Taps come in different varieties, such as hand taps, power taps, and tapered taps, and are marked with the following information:
Nominal Size (Threads/Inch) | Thread Form Designation |
Material Tap is Constructed From | Tolerance for Pitch Diameter |
The nominal size refers to the thread density, and the thread form designation indicates the thread family (e.g., ACME, UNC, UNF, etc.). The material is typically durable, such as carbide, and the tolerance provides a code representing thread precision.
Many confuse clearance holes with tapped holes, but clearance holes are not tapped. They are drilled for the threaded portion of a fastener to pass through, with a nut clamping components together at the opposite end.
Threading refers to the process of creating external threads on a cylindrical fastener like a screw or bolt. These external threads engage with the internal threads in a tapped hole to fasten components together.
Threading starts at the point where the fastener engages the material and runs along the cylindrical body to the shank (the unthreaded portion). Threaded fasteners, such as screws and bolts, have been used for centuries to hold components together. Screws, in particular, act as simple machines, converting rotational force (torque) into linear force, similar to the mechanism of the Archimedes screw.
Pro-Tip: When designing a threaded fastener, it’s often better to use off-the-shelf fasteners. If custom fasteners are necessary, use threading calculations to ensure proper design.
Tapped Hole: A tapped hole is a threaded hole created by tapping to form internal threads.
Threaded Hole vs. Tapped Hole: These terms are often used interchangeably because a tapped hole is simply another term for a threaded hole.
Drilled Hole vs. Tapped Hole: A drilled hole is a smooth cylindrical hole, while a tapped hole has internal threads to accommodate a fastener.
Understanding the distinction between tapped holes and threaded holes is essential for mechanical design. While both terms are often used interchangeably, knowing the correct process behind each term can improve your design’s functionality and accuracy. Whether you’re drilling or tapping, our CNC machining services can produce your custom parts quickly and efficiently.
Upload your design, and experience our fast quoting, manufacturability feedback, and precision machining process. Let us help you bring your projects to life, with parts ready in as little as two days!
Get the latest trends and facts about CNC fabrication from our blog.
Shenzhen Runkey Precision Technology Co. Ltd, a subsidiary of the Tensun Group, is your trusted one-stop solution for custom manufacturing from prototyping to production.Transforming your idea into reality with digital manufacturing resources,streamlined processes, expert guidance,accelerated timelines, and uncompromising quality.
©2024. CNC Fabrication All Rights Reserved.