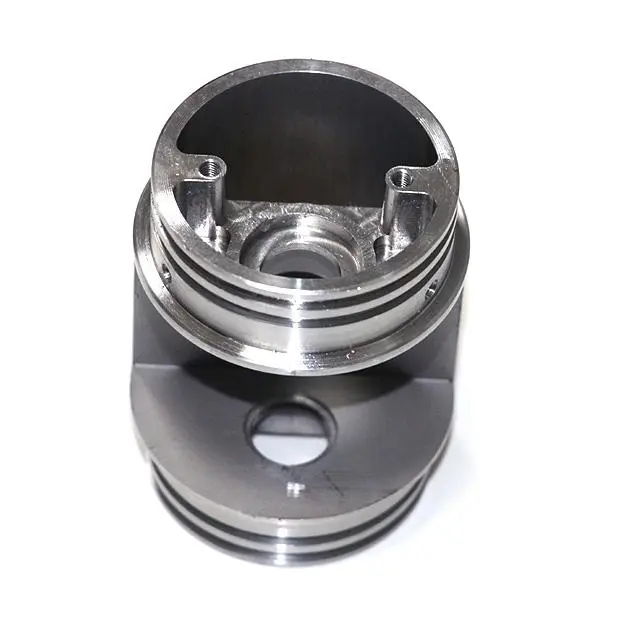
- +8615586668226
- [email protected]
- No. 30, Hongbang Industrial Park, Shenzhen
Heat-resistant plastics are special types of plastic materials designed to withstand extreme heat without degrading. Their ability to endure high temperatures makes them indispensable in various high-temperature applications.
“For environments that turn up the heat, choosing the right plastics is vital,” explains a materials science expert.
To fully appreciate the capabilities of heat-resistant plastics, it’s essential to understand their inherent properties, which include thermal resistance, chemical resistance, and mechanical properties.
Selecting the right heat-resistant plastic material is crucial for any project that involves high heat. Here’s a look at the top five:
Plastic Type | Max Temperature (°C) | Primary Properties |
---|---|---|
PTFE | 260 | Chemical and heat resistance |
PEEK | 250 | High tensile strength |
Polyimide | 300+ | High thermal stability |
PPS | 240 | Chemical and fire resistance |
Polycarbonate | 140 | Impact resistance, good thermal performance |
PTFE is a standout heat-resistant plastic due to its ability to operate at temperatures up to 260°C while maintaining its chemical resistance.
PEEK is highly valued for its robustness in challenging environments, including aerospace and medical devices, owing to its high temperature tolerance and mechanical properties.
High-temperature plastics cover a wide range of applications where thermal resistance and durability are essential.
Injection molding is a common method for fabricating parts from heat-resistant plastics, which requires knowledge of the material’s melting point and thermal properties.
Selecting the appropriate heat-resistant polymer involves considering the operating temperature, environmental exposure, and specific mechanical properties required.
What are heat-resistant plastics commonly used for?
They’re used for making components that must endure high temperatures, like aerospace engine parts and high-performance automotive components.
Can heat-resistant plastics be recycled?
Some types can be recycled, though the process can be complex due to their stability and chemical resistance.
Do all heat-resistant plastics have the same thermal properties?
No, they vary widely—each has its own heat deflection temperature, tensile strength, and thermal resistance.
Are there budget-friendly heat-resistant plastics?
Yes, some like Polycarbonate offer a cost-effective solution with reasonable heat resistance for less demanding applications.
Enhance your production capabilities by exploring our Machining Services, and delve into our potential for CNC Solutions. For precision engineering, visit our Precision Machining and Metal Bending. Discover more with our specialized CNC Milling.
Get the latest trends and facts about CNC fabrication from our blog.
Shenzhen Runkey Precision Technology Co. Ltd, a subsidiary of the Tensun Group, is your trusted one-stop solution for custom manufacturing from prototyping to production.Transforming your idea into reality with digital manufacturing resources,streamlined processes, expert guidance,accelerated timelines, and uncompromising quality.
©2024. CNC Fabrication All Rights Reserved.