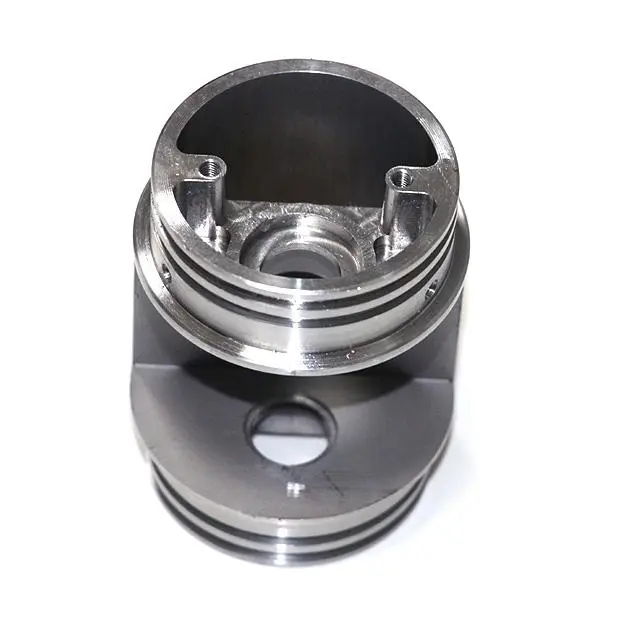
- +8615586668226
- [email protected]
- No. 30, Hongbang Industrial Park, Shenzhen
Each technique has distinct characteristics, advantages, and disadvantages that make them suitable for different applications. Understanding these differences is essential for making informed decisions when designing and fabricating metal components. This article will explore the definitions, pros and cons, and applications of both riveting and welding, helping you choose the right method for creating strong, durable parts.
Riveting is a semi-permanent, non-thermal joining process that employs mechanical fasteners, known as rivets, to connect sheet metal parts. This method involves drilling a hole through the metal pieces, inserting a rivet, and then deforming the rivet’s tail to secure it in place. The rivet’s dome-shaped head and the flattened tail prevent any removal, creating a stable joint.
Riveted joints can be categorized in various ways:
Based on Rivet Placement:
Based on the Number of Cover Plates (for Butt Joints):
Based on Rivet Arrangement:
Pros:
Cons:
Welding is a thermal process that permanently fuses two similar or dissimilar metal parts by melting them together. This process involves aligning the metals, applying heat, and allowing them to cool to form a strong joint.
Pros:
Cons:
Both methods have unique advantages and challenges that influence their suitability for different applications. Here are some key differences:
In summary, both riveting and welding are effective methods for joining sheet metal parts, each with its own strengths and weaknesses. Your choice should depend on various factors, including material types, desired joint strength, weight considerations, and overall costs. By understanding these differences, you can make informed decisions that best suit your fabrication needs. For expert guidance tailored to your specific project requirements, contact our professional sheet metal fabrication service. We prioritize quality and efficiency at competitive prices, ensuring you receive the best solutions for your design challenges. Upload your design file today to receive a quote and DfM analysis within hours.
Get the latest trends and facts about CNC fabrication from our blog.
Shenzhen Runkey Precision Technology Co. Ltd, a subsidiary of the Tensun Group, is your trusted one-stop solution for custom manufacturing from prototyping to production.Transforming your idea into reality with digital manufacturing resources,streamlined processes, expert guidance,accelerated timelines, and uncompromising quality.
©2024. CNC Fabrication All Rights Reserved.