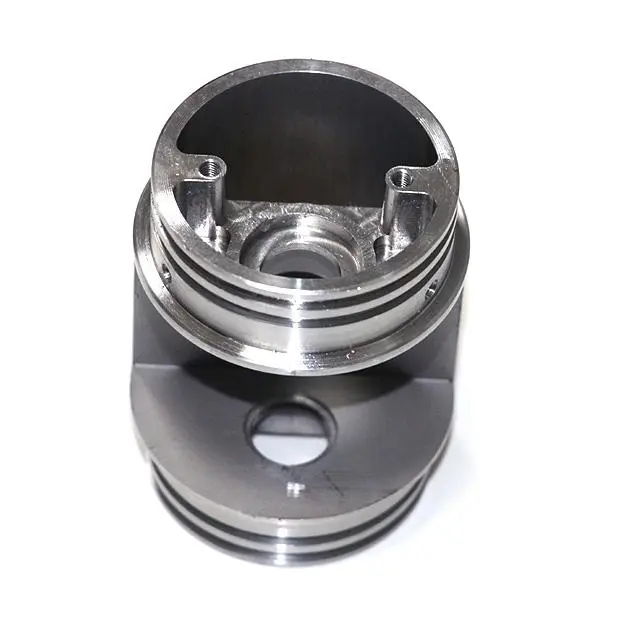
- +8615586668226
- [email protected]
- No. 30, Hongbang Industrial Park, Shenzhen
A CNC milling machine is an advanced piece of manufacturing equipment designed to carve intricate patterns and parts from a variety of materials using computer numerical control. CNC machines are equipped with multiple axes that allow precise cuts through programmed controls.
“CNC milling machines have revolutionized manufacturing, allowing for unparalleled precision and efficiency,” cites an industry expert.
3-axis CNC machines are the most common type found in manufacturing, providing a solid foundation for simple part creation.
Table of Axes Movements in 3-Axis Machines
Axis | Movement |
---|---|
X | Left to right |
Y | Front to back |
Z | Up and down |
4-axis CNC machines introduce an additional rotation around the X-axis, adding more versatility and capability to handle complex shapes.
5-axis CNC machines provide unparalleled versatility, allowing movement along the X, Y, and Z axes with additional rotations around two axes.
7-axis CNC machines are a step further in complexity, offering additional maneuverability that can handle even more sophisticated tasks.
9-axis CNC machines redefine efficiency and complexity by combining milling and turning capabilities without needing additional setups.
12-axis CNC machines represent the pinnacle of precision machining, offering unmatched flexibility and capability.
As CNC technology advances, the precision achievable with additional axes increases, providing superior performance and precision.
Chart: Precision vs. Axes Count
Axes Count | Precision Level |
---|---|
3 | Basic |
4 | Moderate |
5 | High |
7 | Very High |
9 | Exceptional |
12 | Ultimate |
Deciding between a CNC milling machine and a lathe machine depends on the specific project requirements.
Explore how CNC Turning can complement your milling strategies for comprehensive manufacturing solutions.
Why is a 5-axis machine preferred for aerospace components?
They allow precise and complex geometries, crucial for parts that require high precision and durability.
Can I upgrade an existing 3-axis machine to 5-axis?
While technically feasible, converting a 3-axis to a 5-axis machine often involves significant cost and complexity adjustments.
What industries benefit most from 12-axis machines?
Industries like defense, aerospace, and advanced electronics benefit from the intricate capabilities of 12-axis machines.
How does a CNC machine compare to a manual machine in terms of efficiency?
CNC machines offer superior efficiency through automation and precision, reducing manual errors and increasing speed.
Enhance your project with our Machining Services or discover leading-edge solutions through CNC Solutuions. For detailed precision work, explore our Precision Machining and delve into our specialized 5 Axis CNC Machining. Maximize design capabilities with CNC Milling.
Get the latest trends and facts about CNC fabrication from our blog.
Shenzhen Runkey Precision Technology Co. Ltd, a subsidiary of the Tensun Group, is your trusted one-stop solution for custom manufacturing from prototyping to production.Transforming your idea into reality with digital manufacturing resources,streamlined processes, expert guidance,accelerated timelines, and uncompromising quality.
©2024. CNC Fabrication All Rights Reserved.