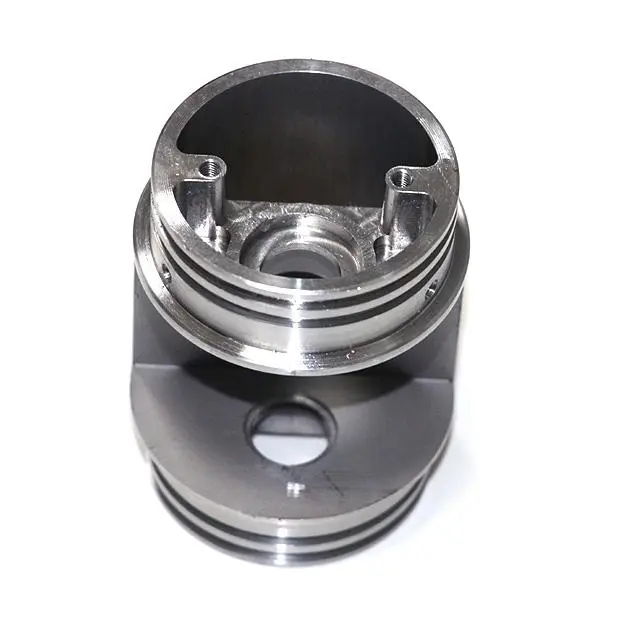
- +8615586668226
- [email protected]
- No. 30, Hongbang Industrial Park, Shenzhen
From the Industrial Revolution to the age of CNC (Computer Numerical Control) machining, machine shops have evolved significantly, adapting to technological advancements while maintaining their core function: producing parts with high precision. This article delves into what machine shops are, their role in modern manufacturing, and their impact on various sectors.
A machine shop is a specialized facility where machining, a form of subtractive manufacturing, takes place. Machining involves using tools to remove material from raw stock (such as metal, plastic, or composite) to create specific parts. Common tools used in a machine shop include lathes, milling machines, and drill presses, each serving a unique function in the production of components with exacting tolerances.
Machine shops have come a long way from their humble beginnings during the Industrial Revolution to the sophisticated facilities we see today.
Machine shops are essential for producing parts used in various industries, including aerospace, automotive, and construction. The main processes carried out in machine shops include:
A well-organized machine shop contains key elements such as:
Machine shops house a variety of machines, each designed for specific tasks:
Machine shops utilize several specialized tools:
CNC machines are at the forefront of modern machining. They are operated by computer programs that control the machine’s movements and functions. CNC technology significantly improves the speed, precision, and repeatability of machining operations, allowing for complex designs and tight tolerances that would be difficult or impossible to achieve manually.
Running a machine shop involves both technical challenges and business opportunities. Key challenges include the substantial investment in equipment, the need for skilled machinists, and staying competitive with emerging technologies. However, machine shops that specialize in CNC services or niche industries, such as aerospace or automotive, can carve out a competitive edge.
Machine shops offer a variety of machining types, each suited to different materials and product requirements:
To ensure precision and high-quality output, machine shops use various inspection techniques:
Safety is a top priority in machine shops. Proper protocols include:
Advanced technologies like AI, robotics, and CNC are transforming machine shops into high-tech manufacturing hubs. AI optimizes operations and predicts maintenance, while robotics enhance precision in repetitive tasks. CNC machines allow for greater design complexity, precision, and efficiency.
Choosing the right machine shop involves considering factors such as:
Operating a machine shop offers several advantages, including precision, speed, and versatility. However, challenges such as high equipment costs, skilled labor shortages, and technological advancements must be managed to ensure continued success.
Machine shops are critical to industries such as:
Machine shops play a vital role in modern manufacturing, providing essential services across numerous industries. With the integration of advanced technologies like CNC machining, AI, and robotics, the industry is evolving to meet the demands of precision, speed, and complexity. The future of machine shops promises further innovations, offering new opportunities and challenges for businesses and machinists alike.
Get the latest trends and facts about CNC fabrication from our blog.
Shenzhen Runkey Precision Technology Co. Ltd, a subsidiary of the Tensun Group, is your trusted one-stop solution for custom manufacturing from prototyping to production.Transforming your idea into reality with digital manufacturing resources,streamlined processes, expert guidance,accelerated timelines, and uncompromising quality.
©2024. CNC Fabrication All Rights Reserved.