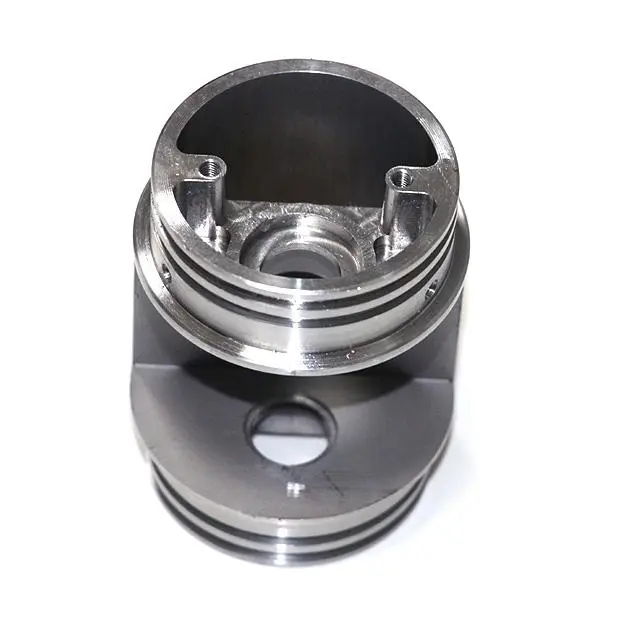
- +8615586668226
- [email protected]
- No. 30, Hongbang Industrial Park, Shenzhen
Aluminum is a versatile and widely used metal in manufacturing, thanks to its lightweight and corrosion-resistant properties. This makes it an ideal choice for various applications, including aerospace, automotive, and medical devices.
Understanding the differences between cast aluminum and machined aluminum can help businesses make smart, cost-effective decisions tailored to their specific needs.
Cast aluminum involves pouring molten aluminum into a mold, allowing it to solidify into a particular shape. This casting process is versatile and cost-effective, perfect for creating complex shapes with minimal machining.
The benefits of cast aluminum, like versatility and reduced material costs, make it a popular choice for many manufacturers.
Machined aluminum refers to aluminum that has been shaped through precise machining using CNC machines. This technique is known for producing high-quality, accurate parts.
The ability to produce machined aluminum parts with exceptional precision makes this method indispensable in industries demanding high performance.
Cast aluminum has some distinct advantages and disadvantages worth considering:
Despite its limitations, cast aluminum remains a viable option for products where cost and time efficiency are paramount.
Machined aluminum offers numerous benefits but also has some downsides:
The precision and accuracy offered by machined aluminum often justify the higher costs in applications requiring reliable performance and durability.
Aluminum alloys are used in both casting and machining, each selected for specific properties and applications.
Alloy | Key Features | Common Uses |
---|---|---|
Aluminum 6061 | Good durability, versatility | Aerospace, automotive components |
Aluminum 7075 | High strength, lightweight | Aerospace, military equipment |
Aluminum 2024 | Excellent strength and hardness | Aircraft structures |
Aluminum 5052 | High formability, corrosion resistance | Marine, automotive fuel tanks |
Choosing the right aluminum alloy is essential for maximizing the strengths of cast or machined aluminum, meeting specific manufacturing process needs.
Deciding between cast aluminum and machined aluminum depends on the project’s specific needs:
Use Cast Aluminum:
Use Machined Aluminum:
Choosing the right material and method can significantly impact manufacturing efficiency and product quality.
The surface finish and tolerance are key considerations when producing aluminum parts.
Deciding between casting and machining directly affects the potential for achieving the final desired quality of the component.
Both cast aluminum and machined aluminum serve vital roles across multiple industries:
The breadth of applications across these sectors showcases the adaptability and preference for both cast and machined aluminum in driving innovation and efficiency.
What makes machined aluminum different from cast aluminum?
The primary difference lies in the production method and resulting properties; machined aluminum is carved from a solid block, offering high precision, while cast aluminum is molded, allowing for complex shapes at a lower cost.
When should one choose die cast aluminum over other methods?
Die casting is ideal for mass production of components with consistent quality, especially useful in the automotive and consumer electronics industries.
Which aluminum alloy is best for strength?
Aluminum 7075 is renowned for its high tensile strength, making it suitable for aerospace and military applications.
Why is surface finish important in aluminum parts?
A quality surface finish enhances the product’s appearance, performance, and protection against corrosion, which is crucial in both consumer products and industrial applications.
How does machined aluminum vs cast aluminum affect aerospace manufacturing?
In aerospace, machined aluminum often offers the necessary precision and strength for critical parts, while cast aluminum helps in producing lightweight components at reduced costs.
At our CNC Fabrication Manufacturing Plant, we provide tailored solutions in machined and cast aluminum, ensuring the right fit for your project needs. Explore:
Ready to make the right aluminum choice for your next project? Contact us to learn how we can assist.
Get the latest trends and facts about CNC fabrication from our blog.
Shenzhen Runkey Precision Technology Co. Ltd, a subsidiary of the Tensun Group, is your trusted one-stop solution for custom manufacturing from prototyping to production.Transforming your idea into reality with digital manufacturing resources,streamlined processes, expert guidance,accelerated timelines, and uncompromising quality.
©2024. CNC Fabrication All Rights Reserved.