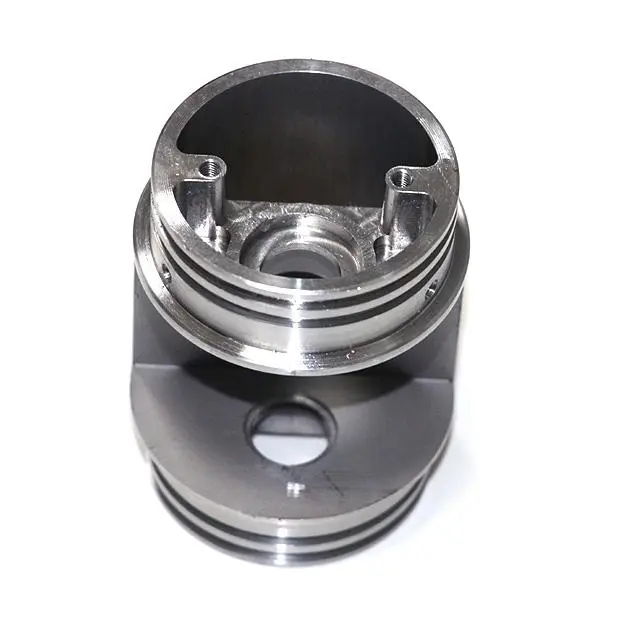
- +8615586668226
- [email protected]
- No. 30, Hongbang Industrial Park, Shenzhen
Boring is a machining process used to enlarge an existing hole in a workpiece. It improves the accuracy of the hole’s diameter and can achieve a high-quality surface finish.
Understanding boring is essential for anyone involved in precision machining processes.
The boring process involves using a single-point cutting tool to enlarge a hole.
This process requires careful control to prevent issues like chatter and deflection.
Several types of boring machines are used in the industry:
Choosing the right machine depends on the specific requirements of the task.
Understanding the differences between horizontal and vertical boring is crucial.
Feature | Horizontal Boring | Vertical Boring |
---|---|---|
Orientation | Spindle is horizontal | Spindle is vertical |
Workpiece Size | Large and heavy | Smaller and shorter |
Common Applications | Engine blocks, turbine casings | Gears, wheel hubs |
Setup Complexity | More complex | Simpler |
Each type offers unique advantages, making them suitable for different machining processes.
A boring machine consists of several critical components:
Understanding these components helps in optimizing the boring operation.
The boring bar is central to the boring process.
Selecting the right boring bar enhances precision and efficiency.
Precision is paramount in boring.
Implementing these practices leads to high-quality results.
Boring offers several benefits:
These advantages make boring indispensable in many industries.
Boring machines are used across various sectors:
Our Machining Services cater to these industries, providing high-precision boring solutions.
To maximize efficiency:
Following these practices enhances both efficiency and precision.
What is the main difference between drilling and boring?
Drilling creates a new hole, while boring enlarges an existing hole to achieve greater accuracy.
Can boring be performed on a CNC machine?
Yes, modern CNC machines can perform boring operations with high precision and repeatability.
What materials can be bored?
Materials ranging from metals like steel and aluminum to composites can be bored using appropriate tools.
How do you reduce chatter in boring operations?
Using a rigid setup, selecting the right boring bar, and optimizing cutting parameters can minimize chatter.
Why choose horizontal boring over vertical boring?
Horizontal boring is preferred for large, heavy workpieces due to its stability and capacity.
At our CNC fabrication manufacturing plant, we specialize in precision boring operations. Serving industries like Aerospace and Aviation, Automotive, and Industrial Equipment, we deliver excellence in every project.
Explore our services:
Ready to elevate your manufacturing process? Contact us today and let’s make your project a success.
Master the art of boring with our expert guidance and state-of-the-art facilities. Together, we can achieve unparalleled precision and efficiency.
Get the latest trends and facts about CNC fabrication from our blog.
Shenzhen Runkey Precision Technology Co. Ltd, a subsidiary of the Tensun Group, is your trusted one-stop solution for custom manufacturing from prototyping to production.Transforming your idea into reality with digital manufacturing resources,streamlined processes, expert guidance,accelerated timelines, and uncompromising quality.
©2024. CNC Fabrication All Rights Reserved.