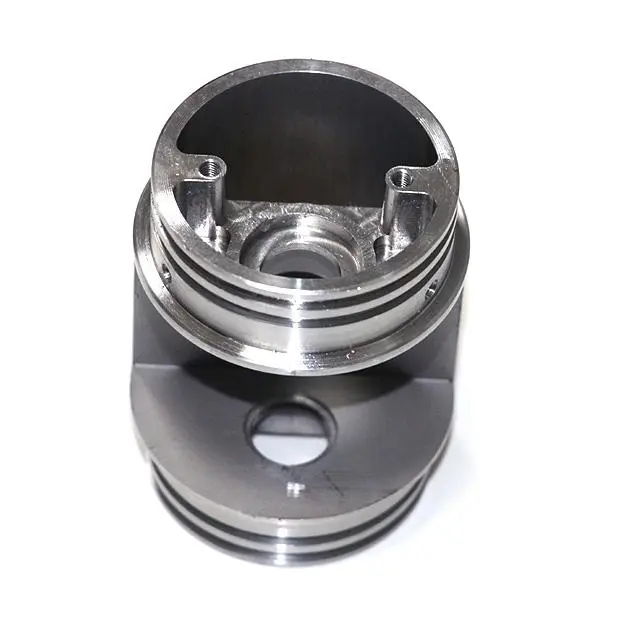
- +8615586668226
- [email protected]
- No. 30, Hongbang Industrial Park, Shenzhen
A CNC lathe is a machine tool that utilizes Computer Numerical Control (CNC) technology to automate the turning and shaping of materials with incredible accuracy. From its humble beginnings to its advanced capabilities today, CNC lathes have revolutionized industries ranging from automotive to aerospace. In this article, we’ll explore what CNC lathes are, their history, how they work, the different types, and the operations they perform.
A CNC lathe is an advanced machine tool that uses computer programming to control the turning and shaping of materials, such as metals, plastics, and wood. This machine integrates traditional lathe principles with computer automation to perform complex tasks with high precision and efficiency. CNC lathes are used in various industries for manufacturing intricate parts and components, and they are essential in machine shops worldwide for their ability to handle a wide range of materials.
The evolution of the CNC lathe began in the mid-20th century. In the 1940s and 1950s, pioneers such as John T. Parsons and Frank L. Stulen, working in the aerospace industry, developed the first numerically controlled machines. These early versions paved the way for the modern CNC lathe, enabling faster, more accurate machining processes that significantly improved manufacturing efficiency.
A CNC lathe works by automating the machining process through computer programming. The process typically includes these steps:
A CNC lathe consists of several key components that work together to ensure precision:
CNC lathes come in various types, each suited for different machining needs:
CNC lathes can perform a wide range of operations, including:
CNC lathe programming relies on various types of software to create and control designs:
CNC lathes are powerful, precise tools that play a crucial role in modern manufacturing. From their historical origins to their current capabilities, they have drastically improved the speed and quality of machining processes. Understanding the types of CNC lathes and their operations can help manufacturers select the right machine for their needs, ensuring efficient production of high-quality parts. As technology continues to evolve, CNC lathes will remain at the forefront of precision manufacturing, shaping the future of countless industries.
Get the latest trends and facts about CNC fabrication from our blog.
Shenzhen Runkey Precision Technology Co. Ltd, a subsidiary of the Tensun Group, is your trusted one-stop solution for custom manufacturing from prototyping to production.Transforming your idea into reality with digital manufacturing resources,streamlined processes, expert guidance,accelerated timelines, and uncompromising quality.
©2024. CNC Fabrication All Rights Reserved.