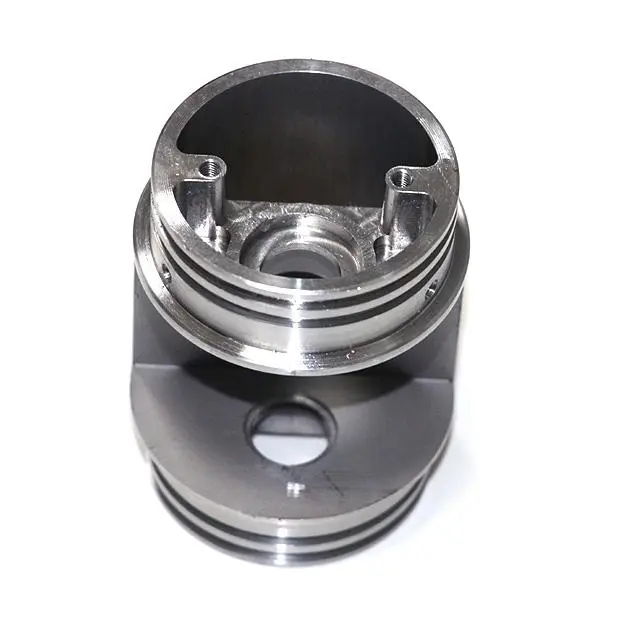
- +8615586668226
- [email protected]
- No. 30, Hongbang Industrial Park, Shenzhen
Aluminum extrusion is a technique where aluminum material is forced through a die to create objects with a fixed cross-sectional profile. This manufacturing process is highly valued for its efficiency and adaptability.
By passing a heated aluminum billet through a die using an extrusion press, extruded aluminum profiles are created, offering the flexibility to produce various shapes and sizes. This is highly beneficial across industries, providing innovative solutions tailored to specific needs.
The extrusion process begins with an aluminum billet being heated to about 400°C to 500°C to make it malleable. Here’s a simplified step-by-step:
The efficiency of this process—alongside advancements in extrusion tooling—has made aluminum extrusions a staple in modern manufacturing.
Various shapes can be extruded, allowing flexibility in design:
Each shape serves unique functions, optimized for specific uses. The ability to create complex cross-sectional profiles without compromising strength is a significant advantage.
Aluminum has become a favored material due to several qualities:
The use of aluminum streamlines processes while offering robustness and versatility, perfect for large-scale manufacturing needs.
Understanding these two methods can help in choosing the best fit for your projects:
Direct Extrusion: The most common method where the billet and ram move in the same direction through a stationary die.
Indirect Extrusion: Involves the die moving relative to the stationary billet. This results in less friction and is suitable for complex profiles.
Both methods have their advantages but must be chosen based on specific project requirements and desired extrusion performance.
In automotive applications, extruded aluminum offers weight reduction without sacrificing strength, enhancing fuel efficiency. Parts like body panels, engine blocks, and structural elements benefit from extrusions’ precision and durability.
A case study shows how leading car manufacturers achieved a 15% weight reduction in car chassis, thereby improving both performance and efficiency.
The aerospace sector demands high precision, which aluminum extrusion delivers by providing lightweight yet strong components. Applications include:
According to industry reports, adopting aluminum extrusion has reduced assembly time by 20%, contributing to cost savings and enhanced safety.
Custom aluminum extrusions allow manufacturers to design without constraints. Here’s how they make a difference:
Download our aluminum extrusion design guide to explore how custom solutions can elevate your projects.
Selecting the right extrusion die is critical for achieving optimal extrusion:
Engaging with experienced fabrication services ensures high-quality dies that meet all technical demands.
How is aluminum cooled after extrusion?
Can complex shapes be achieved with aluminum extrusion?
What is the typical lead time for an extrusion project?
How does temperature affect the extrusion process?
Why is aluminum extrusion popular in automotive design?
To further explore the potential of aluminum extrusion in your projects, reach out to our fabrication experts. Whether you need help with design or manufacturing, our team is here to support your journey towards innovation and excellence.
Get the latest trends and facts about CNC fabrication from our blog.
Shenzhen Runkey Precision Technology Co. Ltd, a subsidiary of the Tensun Group, is your trusted one-stop solution for custom manufacturing from prototyping to production.Transforming your idea into reality with digital manufacturing resources,streamlined processes, expert guidance,accelerated timelines, and uncompromising quality.
©2024. CNC Fabrication All Rights Reserved.